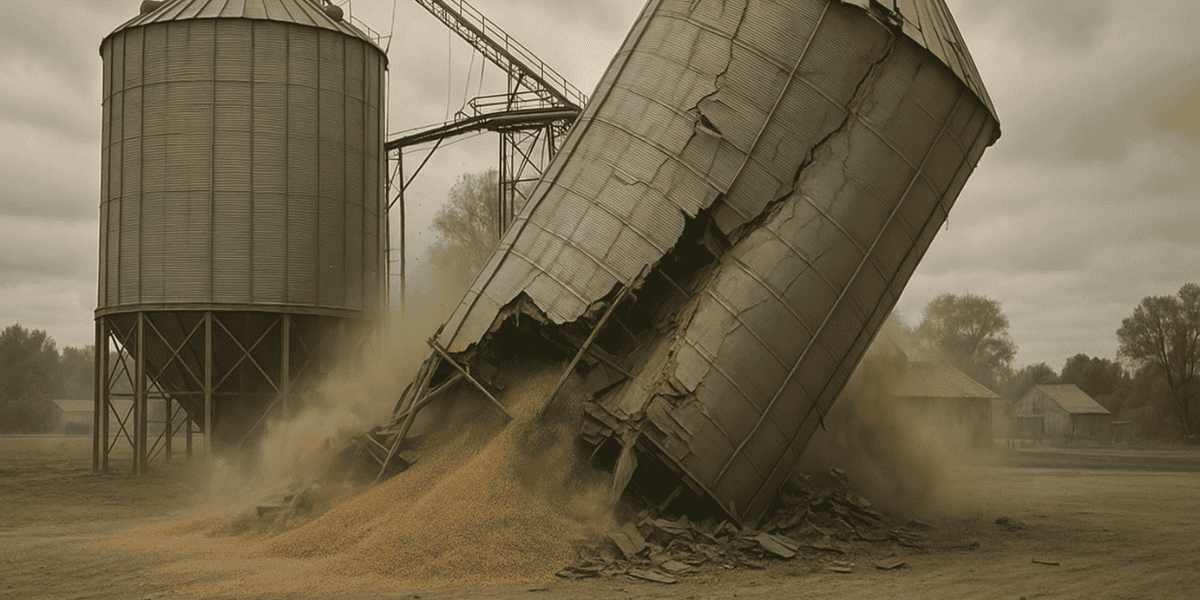
Why Silos Collapse: Understanding Causes, Prevention, and Safety
Silo collapses rarely happen without warning. Early signs, like corrosion, stress cracks, or foundation settling, are often visible but overlooked. When failure finally comes, it’s sudden, devastating, and almost always preventable. In this guide, we’ll cover the top causes of silo failure, the warning signs to watch for, and proven steps you can take to prevent a collapse.
Here is a summary of what we cover:
- Top Causes of Silo Collapses
- Warning Signs Your Silo May Be at Risk
- How a Silo Collapse Progresses Over Time
- How to Prevent a Silo Collapse
- Emergency Response and Planning
- Final Thoughts
Top Causes of Silo Collapses
Silo collapses are rarely the result of a single failure. In most cases, hidden structural weaknesses build up over time until a sudden failure occurs. Understanding the most common causes is critical to spotting early warning signs and taking action before disaster strikes.
Below are the leading factors that contribute to silo failure, and what to watch for in your facility.
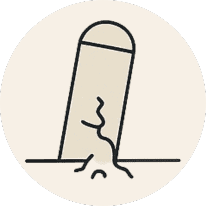
Foundation Problems
A weak or unstable foundation is one of the most common reasons for silo failure. Even minor shifts can cause catastrophic structural instability.
Signs to watch for:
- Cracks in the concrete base
- Uneven settlement or visible leaning
- Erosion or water pooling around the foundation
- Gaps between the foundation and silo walls
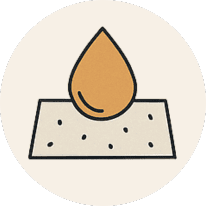
Corrosion and Structural Degradation
Over time, silos exposed to moisture, chemicals, or extreme weather can experience corrosion that weakens their structural integrity.
Key indicators:
- Rust streaks or patches on exterior surfaces
- Peeling or degraded paint
- Thinning or pitted steel around seams and joints
- Holes or visible weakening in metal panels
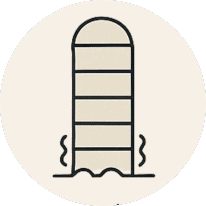
Improper Design or Construction Defects
Flaws in the original silo design or mistakes during construction can create long-term vulnerabilities.
Common issues include:
- Undersized foundations for the silo’s load
- Inadequate reinforcement or bracing
- Poor welding, fastening, or assembly practices
- Failure to account for local soil conditions
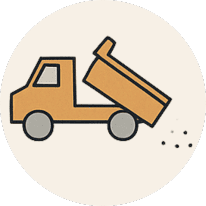
Overloading and Uneven Loading
Filling a silo beyond its rated capacity, or loading it unevenly, can exert dangerous stresses on the structure.
Warning signs:
- Bulging walls or visible deformation
- Unusual creaking, popping, or stress noises
- Irregular settling or cracking at the base
- Blockages during discharge creating asymmetrical pressure
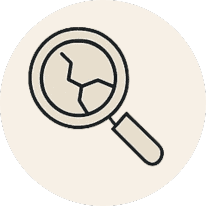
Inadequate Maintenance and Inspections
Neglecting regular inspections and repairs allows minor issues to develop into major failures.
Maintenance gaps to avoid:
- Failing to address small cracks, leaks, or corrosion early
- Ignoring misalignments, buckling, or shifting
- Skipping annual professional structural assessments
- Overlooking foundation damage after heavy rain or floods
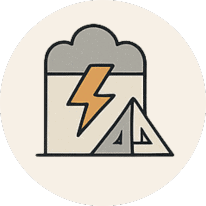
Environmental Factors and Natural Events
Severe weather, flooding, or seismic activity can quickly compromise a silo’s stability, especially if there are already underlying issues.
Risk factors:
- High winds causing structural fatigue
- Floodwaters eroding the foundation
- Temperature extremes causing expansion and contraction stresses
- Seismic tremors destabilizing supports
Takeaway: Most silo failures start with preventable issues like foundation cracks, corrosion, or overloading.
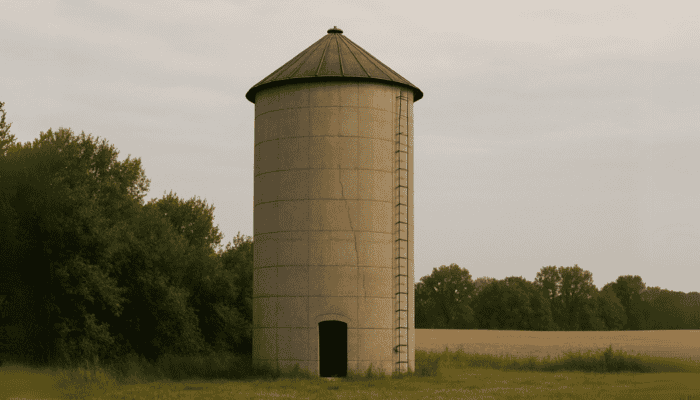
Warning Signs Your Silo May Be at Risk of Collapse
Silo failures often show early warning signs before a major structural event occurs. Recognizing these indicators during routine inspections can prevent costly damage, downtime, and serious injuries.
Here are the most common signs that your silo may be developing structural issues:
Structural Warning Signs
- Cracks in the foundation or visible shifts around the base
- Bulging, dents, or deformations in silo walls
- Doors, hatches, or seals that no longer align properly
- Noticeable leaning or tilting of the silo structure
Surface and Material Warning Signs
- Rust streaks, peeling paint, or exposed bare metal
- Water leaks or signs of corrosion at seams and joints
- Grain leaks from cracks, seams, or at the base
Operational Warning Signs
- Unusual popping, creaking, or groaning sounds during loading or unloading
- Slow or uneven material discharge indicating blockages or uneven pressure
- Excessive dust clouds or material escaping around door seals
Takeaway: Small issues like cracks or minor leaks can signal much larger structural weaknesses. Don’t ignore early warning signs, schedule a professional inspection at the first sign of trouble.
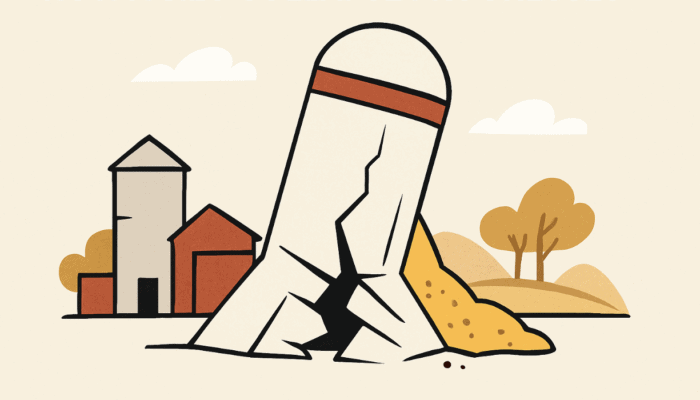
How a Silo Collapse Progresses
Silo collapses rarely happen without warning. In most cases, structural failures build slowly over time, following a predictable pattern. Understanding the typical progression can help you spot risks early, and take action before a complete failure occurs.
Here’s how a silo collapse usually unfolds:
- Early Warning Signs: Small cracks, minor leaning, or visible rust start to weaken the structure.
- Structural Weakening: Over time, load-bearing walls deform, corrosion spreads, and foundation stress increases.
- Visible Deformation: Bulges, dents, or misaligned hatches appear. Strange noises like popping or creaking may occur under load.
- Full Collapse: If warning signs are ignored, the silo may crumple, tip, or burst, leading to massive grain loss and serious facility damage.
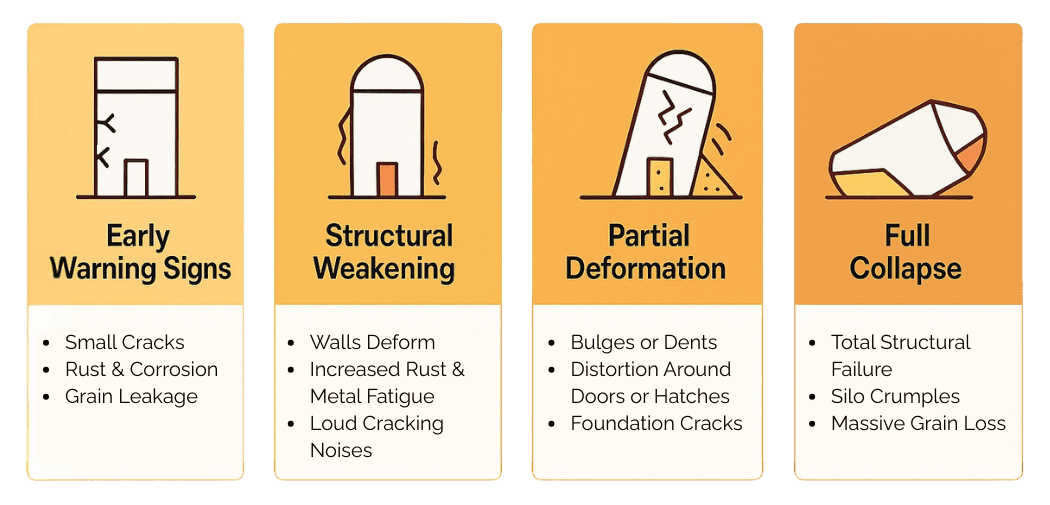
Takeaway: Early intervention, especially when minor cracks, rust, or leaning appear, can prevent a catastrophic silo collapse.

How to Prevent a Silo Collapse
Silo collapses are almost always preventable with the right combination of regular maintenance, safe operational practices, and proactive planning.
Here’s how you can dramatically reduce your risk:
Maintain Your Silo’s Structural Integrity
Routine inspections, cleanings, and timely repairs are the first line of defense against catastrophic failures.
Focus on:
- Performing regular visual inspections for cracks, corrosion, and foundation shifts
- Scheduling annual professional maintenance cleanout and inspection
- Promptly repairing small cracks, rust spots, and degraded seals
- Protecting exposed steel with fresh coatings to prevent corrosion
Operate Within Safe Limits
Many collapses occur not because of obvious damage, but because operational practices overload or stress the silo beyond its design.
Prevent operational stresses by:
- Following safe fill levels and never exceeding capacity
- Loading and unloading material evenly to prevent asymmetric pressure
- Performing regular silo cleanouts to remove built-up material that can cause uneven loading
Plan for Environmental and Emergency Risks
Even the best-maintained silos can be vulnerable to extreme conditions or unexpected failures.
Be ready by:
- Inspecting silos after severe weather events (floods, heavy storms, freeze-thaw cycles)
- Monitoring for subtle foundation shifts after periods of heavy rain
- Developing a formal Emergency Action Plan (EAP) so everyone knows what to do if a structural issue is detected
Takeaway: Routine maintenance, smart operation practices, and proactive planning can dramatically extend the life of your silo, and protect your entire operation from catastrophic losses.
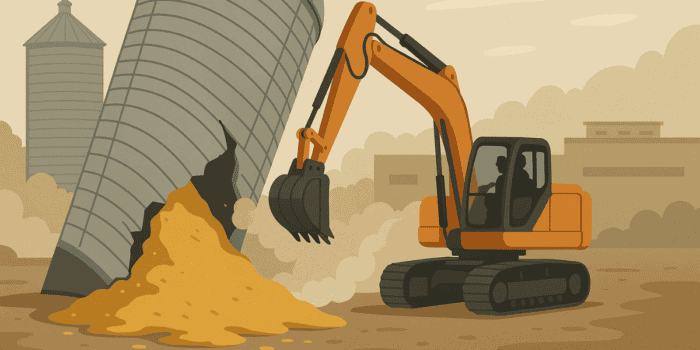
Emergency Response and Planning
Even with proper maintenance and inspections, structural failures can happen without warning.
When they do, having a solid Emergency Action Plan (EAP) and an experienced recovery team ready can make all the difference in protecting lives, limiting damage, and speeding recovery.
Why an Emergency Action Plan (EAP) Matters
A well-developed EAP helps you respond quickly and safely during a structural emergency.
It ensures:
- Clear evacuation procedures to protect employees
- Fast, organized internal communication
- Faster coordination with emergency responders
- Reduced confusion and panic during a critical event
Without an EAP, even minor collapses can escalate into major disasters.
What to Do Immediately If a Collapse Is Suspected or Occurs
If you observe signs of an imminent collapse, or if a failure has occurred, take these critical steps:
- Evacuate the area immediately to protect all personnel.
- Secure the site to prevent further risk to workers or emergency responders.
- Contact emergency services if there are injuries or hazards.
- Follow your Emergency Action Plan to manage communications and safety.
- Do not attempt salvage or recovery operations yourself. Secondary collapses are common and deadly.
- Call West Side Salvage for expert emergency response and recovery assistance.
Note: Attempting to enter or recover material from a compromised structure without professional support puts lives at serious risk.
How West Side Salvage Responds to Collapses
West Side Salvage specializes in emergency response and salvage recovery for silo, grain bin, and tank collapses across the country.
Our process includes:
- Rapid Nationwide Response: We quickly mobilize crews and specialized equipment to your site.
- Site Safety Assessment: Our first priority is human safety. We evaluate the structural risk before beginning any recovery.
- Stabilization of the Scene: We carefully stabilize compromised structures to prevent further collapse before removing material.
- Safe Product Removal and Salvage: We recover as much grain, seed, or product as possible using confined-space-trained crews and specialized recovery equipment.
- Debris Removal and Cleanup: After salvage, we can safely dismantle collapsed silos or bins and prepare the site for rebuild or insurance evaluation.
- Insurance and Engineering Coordination: We work with your insurance adjusters and engineers to document the damage, support claims, and expedite your recovery.
Be Ready Before an Emergency Happens
The best protection is to prepare before an incident ever occurs. West Side Salvage also helps facilities develop customized Emergency Action Plans (EAPs) to minimize response time and protect employees and assets.
Takeaway: Don’t face a silo collapse alone. A clear plan and expert recovery support can protect lives, minimize losses, and speed your facility’s recovery.
Conclusion
Silo collapses are rarely sudden, they build over time through small warning signs, structural stresses, and preventable maintenance issues.
The good news is that most failures can be avoided with regular inspections, smart operational practices, and proactive emergency planning.
By understanding the common causes, recognizing early warning signs, and investing in preventative maintenance, you can dramatically reduce the risk to your facility.
And if a collapse does occur, having an Emergency Action Plan, and a trusted recovery team like West Side Salvage, ensures a faster, safer response when it matters most.
Whether you need routine maintenance, emergency salvage services, or help developing a customized Emergency Action Plan, West Side Salvage is ready to support your operation every step of the way.
If you’re ready to protect your facility and reduce your risk, reach out to us today.